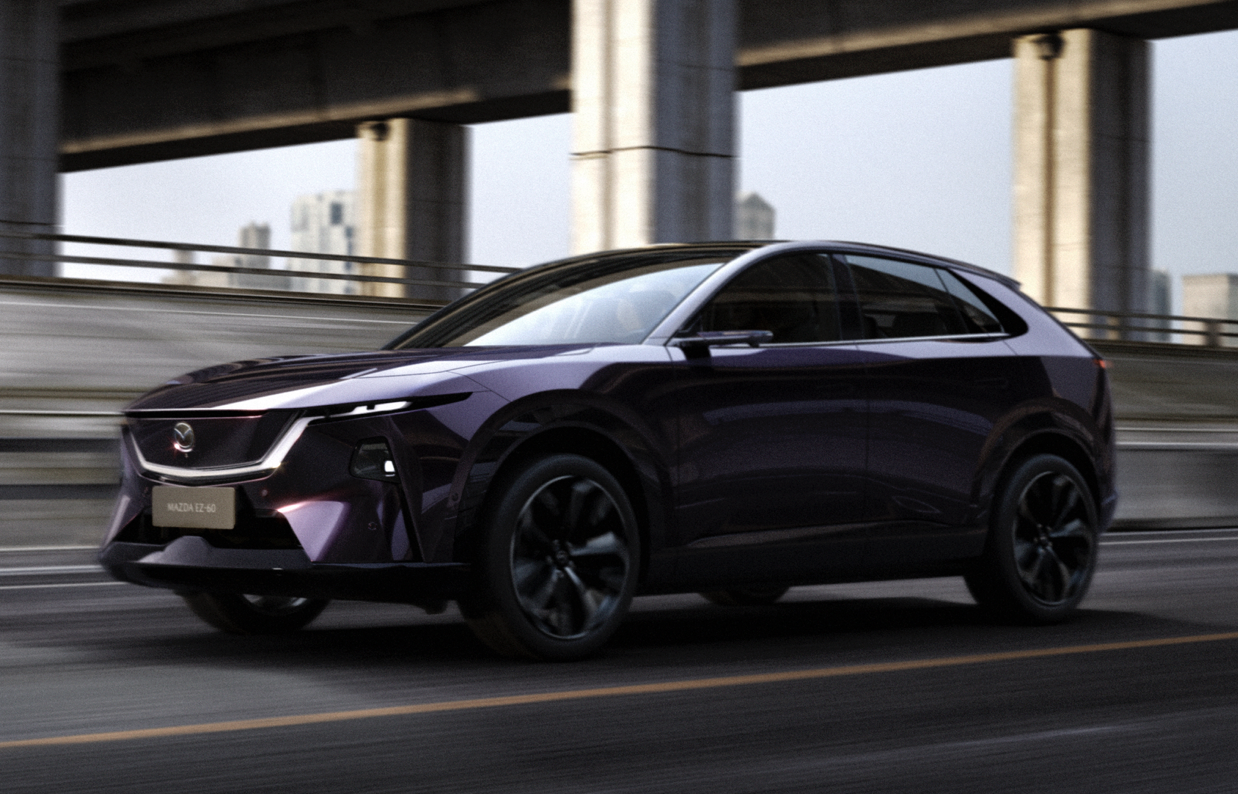
长安马自达MAZDA EZ-60全球首秀
来源:汽车商业评论(刘宝华)21年12月4日 13:43
12月3日,2021中国汽车供应链峰会暨第六届铃轩奖盛典在武汉经开区开幕。为期两天的活动,各类汽车专家、主机厂研发负责人、采购负责人以及汽车零部件企业负责人共计600余人参加峰会。这是中国汽车界最具专业的零部件大型创新交流论坛。
该活动由汽车商业评论和轩辕之学主办,武汉经济技术开发区联合主办,中国汽车电子专业委员会协办,中国汽车工程学会作为指导单位,推动力集团承办。来自20多家主机厂的采购负责人作为铃轩奖评委,500余家零部件企业代表,与主机厂研发人员、各方专家学者,以及其他主流零部件企业代表汇聚一堂。
2天会议包含27场主题演讲,4大圆桌讨论,1个“追芯人”和“被追人”的年度吐槽大会。
第二天大会上午,育材堂科技有限公司董事长兼CTO易红亮带来《以钢降碳》主题演讲。
轻量化是汽车四化之外另一个非常重要的“化”,许多车企以密度更低的铝合金、镁合金替代钢铁材料以实现轻量化。
但在低碳要求下必须考虑更多因素,车用钢铁的全生命周期碳排放只有轻金属的1/4左右。易红亮的结论是“钢铁材料,如果从原材料的获取来看,它就是一个真正意义上的目前我们可选择的最低的碳排放的材料。”
在车身材料领域,目前的一大课题就是在材料本身的碳排放和整车车身的轻量化之间做一个妥协或者做一个重新的思考、新的平衡。
近几十年的解决方案是高强度热成形钢,通过把高强度钢做薄以减轻重量。但其过程产生了给涂装、焊装带来麻烦的氧化问题,20多年前诞生的铝硅镀层技术解决了氧化问题,让1500兆帕的热冲压成形钢得以大规模应用在车身上,占据车用钢的20%—30%。
新技术带来新问题——钢板韧性变差,零部件容易变形。育材堂通过减薄镀层厚度不仅提升了材料韧性,还把强度进一步提高,从1500兆帕提升到2000兆帕。
通过这个新技术,未来几年内可以给白车身带来15%—20%减重潜力,同时镀层从25微米降到10微米给整个钢板制造带来5%碳排放减少,给零部件加工环节带来30%能耗的降低和缩短生产加热时间。
更大的想象空间是,新材料有可能让车身几百个零件缩减为十个左右。基础的材料科学可以像芯片一样改变汽车、改变汽车业。
以下是易红亮的演讲实录。
咱们中国汽车供应链峰会把我们整个汽车制造连接到了一起,我们公司强调的包括这个技术强调的,也是以整个产业链为基础来考虑,任何一个技术的创新如果只是站在自己的维度上来考虑,这样的一个技术创新肯定不能为整个产业链所接受。当我们创造一个技术创新的时候,需要站在整个供应链的体系下,整个产业链的体系下来思考我们这个技术究竟需要什么样的技术、需要什么样的定位。
今天我听到前面所有的报告,可能更多的话题或者说更热门的话题跟芯片有关,大家都是“追芯一族”。但是我这里讲的主题“以钢降碳”,刚才讲到面临新的挑战,可能需要一个低碳材料,当真正意义上的零碳材料出现之前,我们觉得钢铁这个材料在现有的材料体系里面选择,它才是现有的真正的低碳材料。
刚才所有话题都讲到“汽车四化”,电气化、智能化、互联化等等。这里面讲到一个问题,如果说当汽车发展趋势,电气化真正走下去之后,对于整个交通的节能减排,从趋势上是一个大的趋势,是一个非常有利的趋势。但如果我们关注到细节来看,如果我们的电动化真的实现了,对产业链,对车身制造等等会带来什么样新的机遇,这其实不是算是挑战,没有挑战就没有新的机遇。
如果同一个车型,它的燃油版和电动版,当发生了电动化之后,运行过程中的碳排放确实大幅度降低了。但是与此同时,制造过程中所需要的材料,实际上碳排放是增加的,为了适应未来的电动化,更强调制造过程当中的材料所带来的碳排放在整个生命周期中的占比,如果面对未来新能源的汽车,是占比更大了。
我们需要重新思考在车身制造产业链的构架下,哪个环节是应该更有利于我们的碳排放,这里面临一个新的机遇,就是在车身制造环节如何把碳排放降下去,因为它在整个全生命周期当中的占比越来越高。
未来生物材料可降解的真正零碳材料,大自然直接给的材料真正用上车,或者真正承担车身的主要材料,我们能考虑的大部分还是以金属材料为主。金属材料在燃油车时代可能强调的是轻量化,当然轻量化是我们永恒的话题,包括在新能源时代下。但是轻量化的策略,现在从到新能源之后,会发生一定的变化。在之前只要车做得比较轻,运行阶段整车的能耗是大幅度降低的。但是现在车做得轻,运行阶段也会降低,但是车身制造阶段所占的比例太高了。
铝合金、镁合金和钢铁材料,它们的密度,钢铁材料是最大的,7.8,铝合金是2.7,镁合金只有1.8,这些材料如果用在车身上,轻量化来讲,密度低的材料可能有优势。
但如果从碳排放来讲,我们看的不只是这个材料用上去的,还有获取这个原材料所需要的碳,制造这个材料所消耗的碳排放,跟这几个金属材料来比,跟从大自然挖出来的镁矿、铁矿、铝矿,把它变成金属元素本身的时候所需要的碳排放,铁的碳排放只有铝的差不多1/4左右。
制造环节,加工铝、加工铁,怎么样加工所带来的碳排放不是最主要的,最主要的是怎么把氧化铁变成铁,怎么把氧化铝变成铝。钢铁材料,如果从原材料的获取来看,它就是一个真正意义上的目前我们可选择的最低的碳排放的材料。
轻量化也很重要,用钢铁材料,用一个密度比较大的材料,密度比较大的钢铁材料碳排放比较低,但是我们需要材料本身的碳排放和整车车身的轻量化之间做一个妥协或者做一个重新的思考,新的平衡。
钢铁材料能不能够实现轻量化,跟其他材料相比,答案是可以的,若干年来,钢铁材料技术持续在进步,怎么进步的呢?强度从最早的300兆帕,逐渐提高到现在主流的强度级别,是1500兆帕的热冲压钢,甚至未来正在开发的,已经开始有人上车应用的是2000兆帕。
当这个材料做的强度越高的时候,虽然密度很高,但是可以做得比较薄,通过减薄材料的厚度同样可以实现轻量化。所以说只要我的车身材料化持续往前发展,材料技术的持续进步,把钢铁材料的强度逐渐再提高,又能满足车身应用其他所有需求情况下,我们也可以认为钢铁材料也是一个非常好的轻量化的材料。
回到碳中和、双碳目标的体系来看,钢铁材料的技术进步,结合它本身的优势——低碳,如果钢铁材料实现了更好的轻量化,是不是说整个轻量化的选择,轻量化和在碳排放就达到了一个平衡,就是一个最优化的选择,高强度的,更轻量化的新一代的钢铁材料技术仍然可以引领车身制造继续前行,继续把我们的碳排放降到更低的情况。
如果要想实现轻量化,必须用非常高强度的材料,比如现在用的1500兆帕的钢,这个钢因为强度太高了,它的强度跟我们现在用的车载弹簧一个强度,我们把强度跟弹簧一样高的材料,想把它变成车身那么复杂的形状,从车身制造产业链来看是非常困难,或者成本至少是不经济、不舒服的状态。
为什么1500兆帕钢全球那么大的用量,作为车身高强度钢的典范和代表,我们把供应链材料加工的逻辑倒过来了,我是先加热,把它烧红了,最后放到零件里面,把它在比较软的情况下做了冲压成形,把它变成我们所需要的零件形状。
与此同时,通过模具内的快速冷却,把它变得非常硬,这样我们才可以得到一个非常高强度的1500兆帕的汽车钢的零件,不是1500兆帕的汽车钢。
这应该是80年代的原始技术,但是为什么走到今天可以做到那么完美?这里面有一个弊端,烧红了拿出来放到炉子里面冲压的时候,这个钢铁在高温下会氧化,氧化之后意味着放到车上的时候不能满足涂装的性能,不能满足焊接的性能,这个钢是不行的,后面需要做额外的处理。什么技术改变了这个?是1999年的安赛乐米塔尔,全球最大的钢铁公司,发明了一个铝硅镀层技术。
这个技术解决了什么呢?在钢铁表面上镀了一层铝,镀了一层铝之后,在这层铝加热到表面的时候,大家知道铝的熔点可能只有670度,因为它密度比较低,但是我们能够坚持到钢烧红了大概在930度的温度下它仍然能存活下来,不会发生别的变化。是因为这个铝在加热过程中,跟铁发生了化合反应,形成了铝和铁之间的金属化合物,熔点可以达到1170度以上。这是非常巧妙的设计,我们用一个钢铁制造流程,一个流程工业,流程工业意味着高效率、低成本的方式把这个镀层解决了,镀层解决了,加热过程中氧化的问题迎刃而解。
这项伟大的技术创新给我们汽车工业带来了1500兆帕的热冲压成形钢,大批量用到了汽车钢上面。现在为止,这个铝硅镀层的热冲压成形钢在全球每年的销量大概是400万吨左右。400万吨意味着我们整个全球的乘用车可能是6000万辆,汽车钢、板材每辆车可能五六百公斤的水平,也就是说整个汽车钢一共只有2300万吨,一个钢种就占据了这里面的20%—30%,也就是说当今世界能给我们轻量化做出巨大贡献的一个材料,就是我们所有的车都要用到的铝硅镀层的热冲压成形钢。
这个技术听起来非常好,解决了一系列的技术问题,任何技术它都是有技术迭代和发展的过程,这个技术已经出来有20年以上了,它解决了涂装的问题,氧化的问题,什么都很好,但这个技术从它出生到现在还是有一些相对来说需要我们再进一步改善的点。因为这个材料刚才讲到了表面是镀的一层铝,铝的加热过程中会跟铁反应,意味着钢铁材料中的铁原子会扩散到表面跟外面的铝发生反应,形成铝铁金属间化合物。
钢里面的碳原子怎么办呢?钢铁的材料强度都是依赖于碳在钢铁里面才能实现高的强度,才叫做钢。碳原子怎么办呢?外面是铝,铝跟铁的金属间化合物里面不能溶解任何的碳原子。这里面就发现了一个科学点,发现了碳原子会到界面去附集,产生比较脆的一层,碳原子很好,可以提高钢的强度。但是也很不好,强度高到一定程度之后,韧性极差,会导致车身的零部件变形,容易发生失效。
走到今天非常好的技术,我能不能颠覆以前的一些概念和设计,重新去定义这个材料,把它韧性做得更好,去改善新的思路。我们这边通过减薄镀层的厚度,以减少界面的扩散,界面移动少了,材料的附集就少了,这样材料的韧性就提高了。与此同时,材料的强度就可以进一步提高,从1500提到2000兆帕。
材料本身的强度和韧性的提高,从工业级别上来看,每提高20%—30%可能都是一个划时代的意义,不是像实验室所获得的提高了20%—30%可能只是简单的实验室的数据。
通过我们这个技术,确实把碳的附集这一层解决掉了,带来什么效果呢?这是实际测试的结果,通过把碳附集这一层解决掉,这个材料的韧性直接提高20%左右。基于这个20%的韧性的提高,意味着我可以把这个强度再继续提高到2000兆帕,与此同时维持这个材料的韧性跟现在相当,或者现在材料的应用能够带来车身的设计上的更大的自由度,可以把这个材料用得更好。
这个材料通过这个新的技术在未来的几年之内可以给白车身带来的技术大概可以有15%—20%减重的潜力,15%—20%的减重的潜力靠的是把材料的应用减薄了,材料的利用减少了,既实现了轻量化,与此同时我是靠减少了这个材料的应用,理所当然这个原材料的获取我就少了20%。
所以说通过这种方式,我达到了一个新的平衡点,材料利用的减少,轻量化、碳中和,这是一个非常完美的结合点。所以说高韧性的热冲压成形钢对未来的车身技术来讲,是会带来一个新的变革技术。
现在大家更多关注的是国内芯片产业,人车之间的交互作用,这给人类社会从车的角度带来未来的发展,给人类社会带来一个新的用车体验、生活方式改变的颠覆。但实际上所有的这些颠覆都离不开一个基础,基础的平台谁来打造?就是我们这个车无论如何它是由车身构成的,只不过车身技术相对比较成熟,未来的世界探索可能挑战性更大,但是并不是说车身技术就不需要再去改进一个基础的平台技术。如果这个车身技术的改进希望给这个车身带来更大的平台,让汽车厂忘掉车身技术的事,你们去做更专业、更改变人类社会未来的事情,基础的事情我们把它做得更完美一些,通过材料技术的创新。
除了性能之外,还有很多因素,比如说耐蚀性能,如果耐蚀性能达不到主机厂的要求,意味着这个材料永远用不上车的,还有包括我们这里讲到的电铸点焊。
上面讲到了新时代电气化、电动化之后,我们在轻量化和低的碳排放之间寻找一个新的平衡点,通过钢铁材料,一个低碳材料,我们通过新的技术创新,实现了轻量化和获取这个材料的轻量化所获得的一个新的平衡点。
再来关注材料本身有没有别的一些能给这个产业链的低碳带来新的优势?首先,我们这个高韧性的材料,我用的这个铝的镀层比以前减薄了,以前是25微米,现在是10微米的镀层厚度。从25微米降到10微米铝的镀层,刚才讲到铝元素从氧化铝变成铝,它本身获取它所需要的碳消耗非常高,如果把表面的铝硅镀层只是降低了铝的镀层,给整个钢板的制造带来了5%碳排放的减少。
第二个方面就是加工方面。热冲压成形,以前因为铝的合金含量比较高,我们需要更长的加热时间,因为铝需要液化,铝跟铁之间反应需要吸热,正常来讲,以前的铝硅涂层板镀层比较厚的时候,给生产制造端带来了30%的能耗增加,我们通过把这个镀层减薄之后,把这30%的能耗增加降低下来了。这个是从能耗的角度,从成本的角度,以前的炉子40米长,如果做同样的东西,现在是30米长就能够解决问题,对制造环节进一步成本的降低,也是制造环节碳排放的下降。
这是我们实际做的,也是率先发现了考虑到了铝镀层对吸热、放热的影响,通过科学的基础的数据,包括实验室的,包括在工业化验证过程当中产业链上验证下来的,确确实实这个镀层减薄带来了30%能耗的降低和缩短了生产加热的时间。
下一个方面是车身制造,现在只是讲到材料的基础问题,材料到车身还有一个加工的问题,马斯克在特斯拉做了大铸件的铝合金压铸件,把后围做成一个铸件。为什么做这个事情?他是技术员的时候就问下面人说,我看到人家做玩具车的很简单,冲一下,一个铸造出来,一个车就出来了,为什么我们造这个车这么复杂?你们能不能腾出我的手脚来让我做自己感兴趣的事情,把制造方面比较简单的事把它处理好,更简单化、集约化。
马斯克的这个大铸件就是基于这个基础思考逻辑,能不能把车身制造一个传统的工艺做得非常简单,不要再让做车的人,车企大部分的精力还投入到去做过去的事情,就是车身的一些事情,实际上特斯拉实现了这个大铸件,它的工程难度在哪儿呢?从小做到大,中间一定有它工程的瓶颈。
我们再从头来看,以后用铝的车身可能跟成本有关系,跟碳中和有关系,意味着钢还是这个车身比较主流的材料。我们问自己另外一个问题,能不能把做钢铁材料真正的白车身,真正的车身制造也变得像做玩具车一样简单,几下一个车就出来了。
这里有一个基本的准则,如果我们做到车身材料的冲压所有的方方面面做到集成化、简约化,一个车身一百多个零件,甚至两三百个零件,如果把整个车身做成十个零件,是不是意味着做车身它的简单程度就跟现在做玩具车一样简单了。
所以我们从车身角度,材料是一个基础,有了这个材料基础,能不能利用现在的创新形成的新的材料对车身制造带来一个变革性的作用。如果说我能把所有的板子很好地拼接到一起,一次性冲压出来就是这个零件,未来一个车可能就十个零件。如果做整车制造的,三百个零件好不好管理?很难,三百个零件好不好焊装、生产?制造难度大不大?肯定是很大的。如果说我们这一切都实现了呢,一个车十个零件,我相信所有车身制造的事全部解决好,让主机厂更多关心人类的未来,把车身的人机互联的这些事情做得更好、更完美。
每一个美妙的故事里面其实工程上都有一个巨大的难题,要不然我们早就做了。这个巨大的难题是什么?刚才讲到了这个材料是表面上镀了一层铝,镀了铝之后,如果把这两张板拼接在一起,通过激光拼焊会发生什么?材料上镀层当中的铝势必要进到焊缝中间去,铝跟钢之间,铝进到钢里面之后会大幅度降低钢铁材料的强度,焊缝会弱化,是因为铝会污染焊缝,导致焊缝是不行的。
现在怎么解决这个事?有两种技术方案,一种是国际上比较主流的,把表面的铝去掉;另外一种,既然铝多了,我能不能放一些中和掉铝的负面元素,要么增加新的成分在焊缝里面去做处理,要不然是削掉、处理掉这个焊缝,但不管是增还是减,咱们产业链都有一个准则,反正多了这个工艺步骤都会带来了一个问题,成本大幅度的增加,增加多少?这个可能比常规的直接镀层拼焊,至少做了这个拼焊比现在不做拼焊的散件拼装成本是大幅度提升了,所以汽车厂一直不用它,或者用量非常小。
如果这个突破了呢,如果说我们把这个激光拼焊做得便宜到成本一分钱不增加,跟现在直接做这个车身零件一样了,又做到了十几个零件拼成一个,对未来车身制造会带来一个变革性的影响。如果这个材料本身的镀层就薄了呢,意味着要么可以直接焊了,要么是焊接过程当中处理非常简单了。通过这样一个创新把整个产业链整合到一起,我相信未来的车身制造变得既简单又便宜,给主机厂带来一个非常重大的变革。
总结,我们这个钢,新的技术我们叫AluSlim,Slim是瘦的意思,碳瘦身了,碳少了,铝用少了,钢板用薄了,白车身实现了节能减排轻量化。这里面不管从哪个方面,从材料本身的获取,从技术发展的规律往前走,也包括钢自身低碳的优势,也包括生产过程中通过制造过程也能降低碳排放,通过焊接降低了焊接的拼焊的门槛,为整个车身制造做到简约化、集成化,让大家更多的精力关注到人类未来的世界。
谢谢大家!